ステップ1 まずは、物流現場の4S推進
4Sとは、整理・整頓・清掃・清潔の頭文字をとったもので、
これに躾けを加えて5Sともいいます。関連HPへ→整理:要るものと要らないものを分け、要らないものを処分すること。
倉庫の中にある販促品や店舗の什器・備品など商品以外の不要なものが驚くような量があるものです。
これらをを整理することが在庫管理の第1歩となります。
整頓:要るもの、倉庫に置くべきものだけを、決められたルールに従い、あるべきところに置くことをいいます。
清掃・清潔:特に食品を取り扱うような場合、食品衛生法やHACCPに則った管理が必要となります。
安全管理といった視点からも4S・5Sは欠かせません。
ステップ2 倉庫にあるものを全部チェックする(整理する)
商品を棚卸しの要領で品目ごとに数え上げる。
商品以外のものは、それぞれ管理責任のある部署に報告し処分させる。
尚、梱包材料などで使う予定のあるものは1ヶ所にまとめておく。
ステップ3 各商品の内容をチェックする
商品について、製造日付・賞味期限などをチェックし、もう出荷できないものは、
産業廃棄物として適正に廃棄処分する。
中には、著しく在庫量の多い商品も出るが、この段階ではそのままにしておく。
ステップ4 最初に、通路や機材・資材置き場から決める
倉庫の床に、フォークリフトやハンドリフト、台車・パレットが通れるか確認しながら、
通路を決めてテープで区画する。
この時に、フォークリフト、ハンドリフトやパレット・梱包材料などを置く場所を決めてします。
ステップ5 商品保管の所番地(ロケーション・コード)を決める
通路以外の部分を、テープで区切って、商品保管の所番地を決める。
ラック(棚)を使っている場合も同じである。
商品の所番地であるロケーション・コード付けの手順は以下のとおり。
@ ゾーンのコードを決める
A 棚の列のコードを決める
B 棚の奥行きのコードを決める
C 棚の段コードを決める
これで、各棚ごとのロケーション・コードが以下のように「ゾーン→列→奥行き→段」の順で決まる。
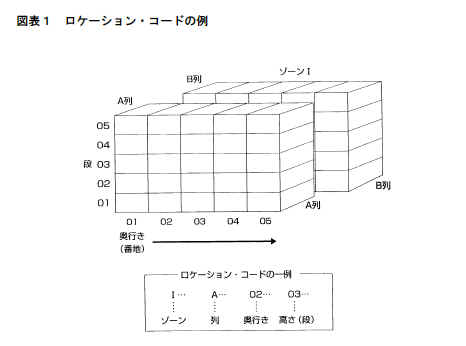
保管にはラック(棚)を使用します。ラック(棚)を使用すると、空間を効果的に利用できます。
一般的には、保管可能な面積は倉庫全体の約45%で、半分以上は入庫・出庫のための仕分け場と通路です。
ステップ6 商品ごとの置き場を決める(整頓する)
入出荷担当者の経験と感覚でよいから、よく動く商品(A・Bランク商品)を出入り口近くに、
あまり動かない商品(C商品)を出入り口から離れたところに置きます。
著しく在庫量の多い商品は、入出荷担当者が「当面は十分」と思う量を置き、
それ以外は出入り口から離れた別のところに置きます。
同一商品内での並べ方は、製造日付の古いもの(賞味期限が早くくるもの)を手前にして、
先に出荷できるようにする。
ステップ7 荷役機器・梱包資材などは、予め決めた場所に置く
フォークリフト・ハンドリフト・台車、パレット・梱包材料を予め決めた場所に置く。
使ったら、必ず決められた置き場に戻すルールを全員で守る。
通路に置かれた機材や資材は無用の障害物でしかない。
いざ出荷になって、台車を探して倉庫の中を走り回るのは時間のムダである。
ステップ8 ロケーションをコンピュータに登録する
以上の置き場所(ロケーション)をリストにし、コンピュータに入力する。
ステップ9 入出荷ごとに、必ずコンピュータに入力する
入出荷のあるたびに、必ず記録を取って、コンピュータに入力する。
ステップ10 ロケーションの適否の見直し・検討
取扱い品目の変更、季節商品の入れ替えなどがあるので、一定期間経過後、
ロケーションの適否についての見直し・変更を行い、最も効率のよい方法にしていく。
その場合でも、作業者の意見を必ず聞く。
「似たような外装の商品が隣り合って置いてあると、誤ピッキングする」など、
現場でないと分からない情報を大切にする。
|